Tackling the challenge of effective heavy oil measurement
By: Craig Marshall, flow measurement consultant at TÜV SÜD National Engineering Laboratory
Tackling Multiphase Flow Measurement in Heavy Oil
Cost-effective heavy oil production is an important objective within the oil and gas industry. Over two thirds of the world’s recoverable oil reserves are classified as heavy oil and bitumen, and with increasing energy demands there comes an increasing demand to produce these fluids. The definition of heavy oil is based on the fluid density and typically covers the API gravity range between 10 and 22, with API gravity greater than 22 representing a more conventional oil density and any less than 10 (the API gravity of water) considered ‘extra heavy’. Although not defined by the fluid viscosity, heavy oils have an associated higher fluid viscosity than conventional oils which, in general, trends inversely with API gravity.
Extraction and processing of high viscosity oils generally comes at a much greater cost. Refining of additional bi-products, contaminant removal and enhanced recovery techniques are needed to maximise recovery. For example, steam is used to heat and therefore reduce the in-situ viscosity of the oil in the reservoir to enhance flow and boost recovery.
Although enhancing recovery rates, chemicals and steam can cause unwanted side effects during heavy oil production. In the case of steam, the added water is often produced with the oil, increasing the likelihood of forming emulsions and produced water challenges once separated. For emulsions, these can often cause separation issues, through long oil-water residence times and the similar fluid densities of oil and water. In addition, this can also result in contamination issues in the separator outlet streams. Using test separators to measure production rates can become ineffective and is regarded as an impractical approach.
The multiphase flow meter (MPFM) is another technology that could support the production of heavy oil fields. MPFMs have been in use for over 20 years and are often considered a valuable addition to new and existing oilfield installations worldwide. The device can be employed onshore, topside and subsea (often directly at wellhead) to deliver a full three-phase measurement of the components within the produced stream (gas/oil/water) and their respective flow rates. MPFMs therefore offer various advantages: real-time production monitoring; improved well testing capacity; and as a full replacement to the conventional test separator setup, thus vastly reducing CAPEX & OPEX costs. However, very few MPFMs have been designed specifically for use with high viscosity oil.
Accurate flow measurement of high viscosity oils is essential for their continued growth in the oil and gas industry and for securing a valuable world energy resource. Flow metering is commonly used to dictate custody and fiscal asset allocation as well as providing well monitoring data for production optimisation. Heavy oil measurement is more complicated due to the effect of fluid viscosity on flow meter performance. In addition, heavier oils are often forced out of the reservoir using water flooding techniques, leading to increased likelihood of oil-water emulsification formation; a new measurement challenge in itself.
Effective Measurement of Heavy Oil
The effect of high viscosity oils on flow metering technologies has been the focus of several research projects at TÜV SÜD National Engineering Laboratory’s Flow Measurement Facility over the past 10 years. This research has revealed that high fluid viscosity introduces significant measurement uncertainties which require correction. It is not simply a case of calibrating in less viscous fluids and using those corrections.
Dynamic qualification is used to identify the optimum performance of the device in controlled conditions and to assess the various measurement processes within the device. This includes analysis of the direct bulk measurement, typically through a Venturi differential pressure flowmeter, and phase fraction measurements, with techniques based on densitometry, electrical or microwaves being most common. This is followed by a mathematical model, calculating the different phase velocities and potentially those same flows at standard conditions through knowledge of composition. Knowledge of the fluid properties are vital in nearly every step of this calculation process.
Multiphase Testing
We conducted an experimental programme investigating flows of high viscosity multiphase mixtures. The nature of the developed flow patterns and performance of a simulated MPFM was assessed. The testing was performed in their multiphase flow facility using high viscosity oil (1500 cP).
The pipeline equipment included a vertical PERSPEX Venturi tube and additional straight length pipe spools to allow for flow visualisation. A high-speed tomography system was installed upstream of the Venturi tube to enable cross-sectional imaging of the flow pattern.
This test, alongside previous heavy oil multiphase trials, has proven substantial fluid viscosity effects, where the conditions prevent gas coalescence, as well as eradicating high frequency slugging and other flow dynamics that would typically be encountered in lower viscosity conditions. Consequently, the variation in flow pattern at the meter inlet, Reynolds number effects, and phase slip, influence the performance and uncertainty characteristics of the simulated meter. Further high viscosity trials with commercial MPFMs have also been conducted. These trials have proved valuable, enabling the manufacturers to establish critical correction data to adapt their MPFM to heavy oil multiphase flows.
To progress the functionality of MPFMs for use in high viscosity flows, we should expect to see more qualification testing in heavier oils. In addition, there is a growing market need, not just for full MPFMs, but for water cut meters and other component devices. These devices need independent qualification under representative conditions. Our research found that the flow dynamics will change between lighter and heavier oils, adversely impacting the device measurement uncertainty if unaccounted for. Further guidance on qualification testing requirements should be proposed to ensure the multiphase flow meter will be tested in suitable conditions that better reflect its baseline performance.
KEEPING THE ENERGY INDUSTRY CONNECTED
Subscribe to our newsletter and get the best of Energy Connects directly to your inbox each week.
By subscribing, you agree to the processing of your personal data by dmg events as described in the Privacy Policy.
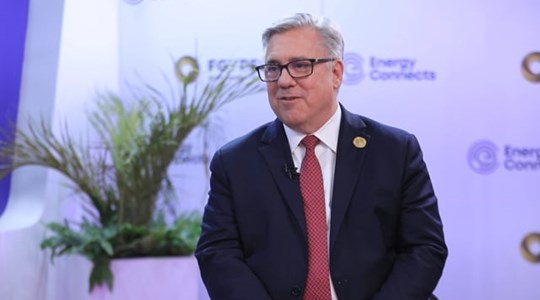
Chevron helping drive Egypt’s journey to become Africa’s energy powerhouse
Mar 11, 2024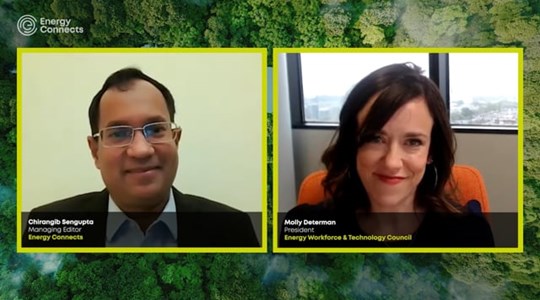
Energy Workforce helps bridge the gender gap in the industry
Mar 08, 2024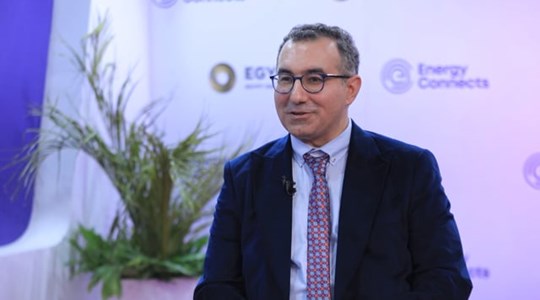
EGYPES Climatech champion on a mission to combat climate change
Mar 04, 2024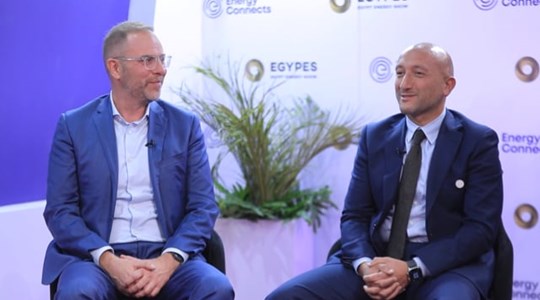
Fertiglobe’s sustainability journey
Feb 29, 2024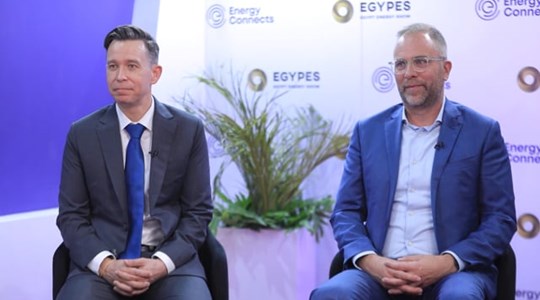
P&O Maritime Logistics pushing for greater decarbonisation
Feb 27, 2024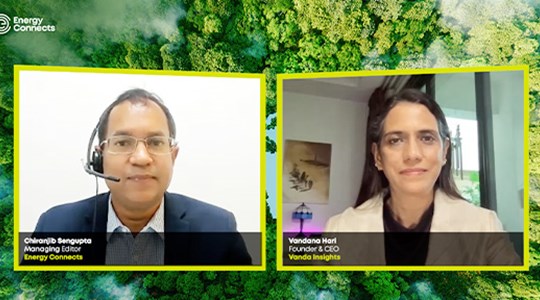
India’s energy sector presents lucrative opportunities for global companies
Jan 31, 2024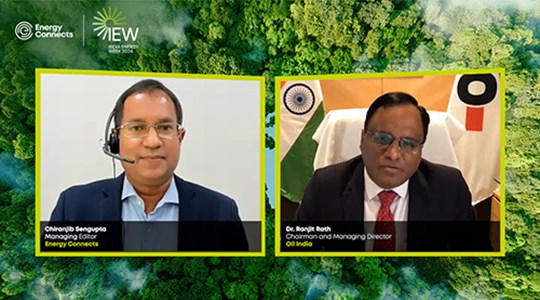
Oil India charts the course to ambitious energy growth
Jan 25, 2024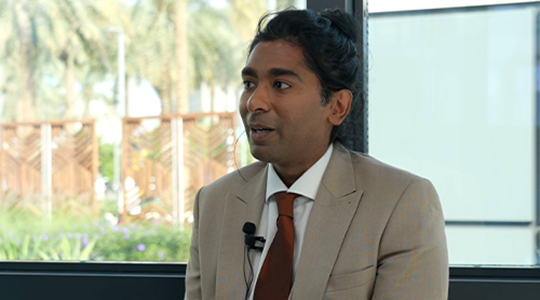
Maritime sector is stepping up to the challenges of decarbonisation
Jan 08, 2024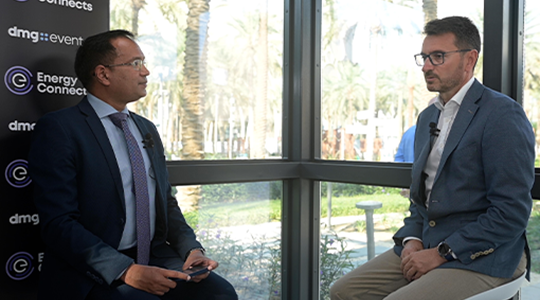
COP28: turning transition challenges into clean energy opportunities
Dec 08, 2023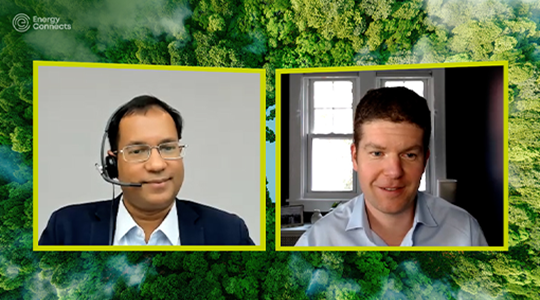
Why 2030 is a pivotal year in the race to net zero
Oct 26, 2023Partner content
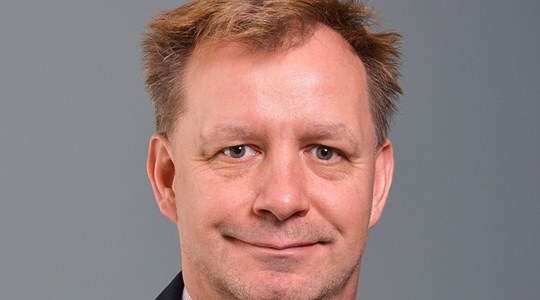
Ebara Elliott Energy offers a range of products for a sustainable energy economy
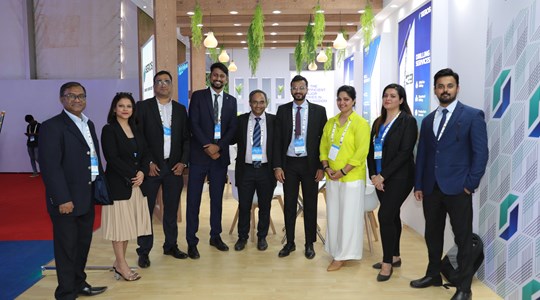
Essar outlines how its CBM contribution is bolstering for India’s energy landscape
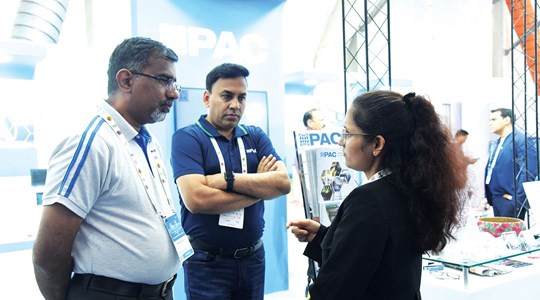
Positioning petrochemicals market in the emerging circular economy
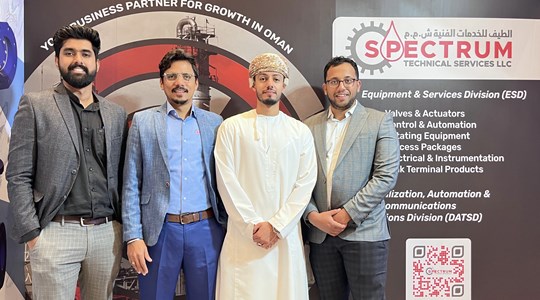
Navigating markets and creating significant regional opportunities with Spectrum
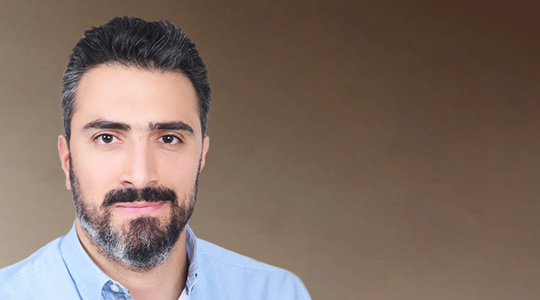