Technologies that can help the oil and gas industry decarbonise
Paolo Danesi, Commercial Director at Exergy International, talks exclusively about the technologies already available on the market that can help the oil and gas sector decarbonise and why Organic Rankine Cycle (ORC) is the ideal technology to recover waste heat.
In its report “Emissions from Oil and Gas Operations in Net Zero Transitions” released in May 2023, the International Energy Agency quantifies the emissions produced by the oil and gas industry in 2022 as 5.1 billion tonnes (Gt) CO2-eq, representing around 15% of the total energy-related greenhouse gas (GHG) emissions. The IEA also highlighted how these emissions should fall by 50% by the end of this decade to be on track with its NetZero Emission by 2050 Scenario.
To curb its emissions by 50% will require the oil and gas industry to invest US$600 billion by 2030 in technologies and certain measures:
- reducing or eliminating methane emissions
- electrifying upstream facilities
- installing carbon capture and storage systems
- increasing energy efficiency of the processes
- expanding hydrogen applications
Technologies to tackle some of these target actions are already available on the market and are ready to be implemented in a cost-effective way to start decarbonising the sector now.
The recovery and utilisation of waste heat produced as a by-product of the oil and gas processes, is today an effective and viable opportunity for the industry to address the need of energy efficiency improvements.
The potential of exhaust-heat recovery from oil and gas processes is sizable, considering that gas turbines reject roughly 50% of the energy in the fuel into the atmosphere through their exhaust systems.
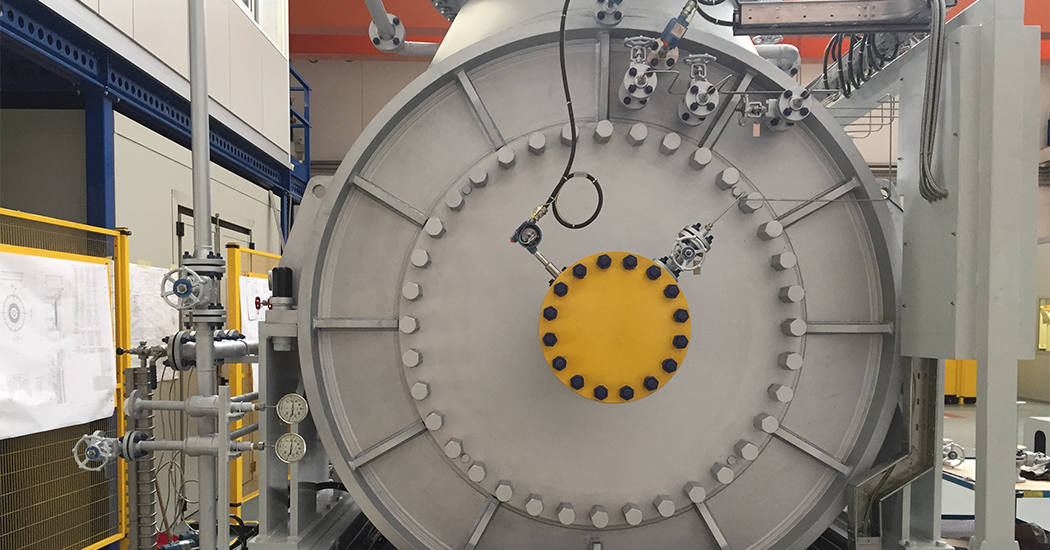
Organic Rankine Cycle
When it comes to recover waste heat from low to medium-high temperatures, to convert it into carbon free electricity, Organic Rankine Cycle is the ideal technology.
An Organic Rankine Cycle (ORC) is similar to the traditional Steam Rankine cycle widely employed in power station; it differs for the use of organic substances instead of water as working fluid for the cycle. This allows ORCs to be more flexible than steam cycles, more efficient to exploit low and medium-high temperature resources and for small power output.
Exergy International, one of the leading suppliers of ORC systems worldwide, introduced in 2010 an innovative turbine, the Radial Outflow Turbine, applied to the ORC cycle, proving even more efficiency and flexibility of these systems, setting new standards for the ORC industry.
For the oil and gas sector the possibility to recover waste heat by using ORC systems are various as Danesi explained: “The more common application of an ORC Waste Heat Recovery system is in gas turbines driving compressors in use in pipelines. One ORC unit can be applied to multiple gas turbines driving the station, so one single ORC power plant can increase the power output by up to 40% and, therefore, reduce the use of fossil fuels to drive the compression”. But this is not the only advantage to consider. Paolo continued: “Gas compressor stations are often located in isolated, sometimes even remote areas, with limited access to water supplies and frequently operate remotely without a permanent staff on-site. Applying an ORC system, instead of using a steam Rankine cycle, has no impact on these restraints as ORC can work without water and does not need any operator on-site, it is a fully automated system remotely controlled.”
ORCs can be efficiently employed also for efficiency improvements in LNG regasification terminals. Here it is possible to recover the waste heat from downstream gas turbines used for compression, and produce additional carbon free electricity, thus making the regasification process more sustainable and efficient. As example “in a project supplied for a PTT LNG regasification terminal in Thailand, at Rayong, exploiting the waste heat from 2 Solar Mars 100 gas turbines we were able through our ORC to deliver 5 MWe of clean electricity,” explained Danesi.
But this is not the only possible application in the LNG sector. Also, the potential of the cold energy available from LNG regasification process can be efficiently leveraged. A recent R&D development from Exergy relates to the design of a Cold Energy plant (CEP). Danesi noted: “We’ve worked years to develop a highly efficient cold energy plant (CEP) based on ORC technology, which regasifies liquified natural gas and converts the heat absorbed from sea water into electricity by recovering the valuable exergy content of LNG.”
The CEP system designed by Exergy achieves high efficiency thanks to the use of the proprietary Exergy Radial Outflow Turbine combined with a Multilevel Condensation Cycle, maximising the revenue from electricity production.
“This is an interesting market for the application of our technology and we estimate that around 2.5 GWe could be produced from recovering the unexploited cold energy potential existing,” he added.
Exergy has also worked to develop another application for the gas sector specifically for gas pressure let-down station.
In pressure let-down stations, natural gas pressure must be decreased to distribution network pressure.
“In this process, potential energy, available as high-pressure difference, is completely lost in the lamination process through a valve. This waste energy can be efficiently recovered by Exergy’s Gas Expander to produce zero emission electricity,” noted Danesi.
Exergy has designed a natural gas expander system that integrates into existing pressure-let down gas stations to increase the efficiency and sustainability of gas distribution systems.
In conclusion, Organic Rankine Cycle is a flexible solution easily adaptable and integrable in several processes in the oil and gas industry such as gas compressor stations, gas pressure let-down stations, LNG regasification processes and also refining and petrochemical to recover waste heat potential available and not utilised. A viable and efficient way to make oil and gas operations more efficient while also reducing their carbon footprint. With a short time to market – 12 months average to install a system - and relatively short return of the investment. Both good reasons to consider ORC solutions to start decarbonising the sector by now.
For more information, please visit www.exergy-orc.com
KEEPING THE ENERGY INDUSTRY CONNECTED
Subscribe to our newsletter and get the best of Energy Connects directly to your inbox each week.
By subscribing, you agree to the processing of your personal data by dmg events as described in the Privacy Policy.
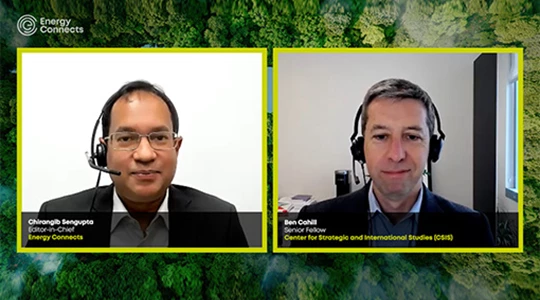
CSIS: long-term LNG demand to reshape global export capacity growth
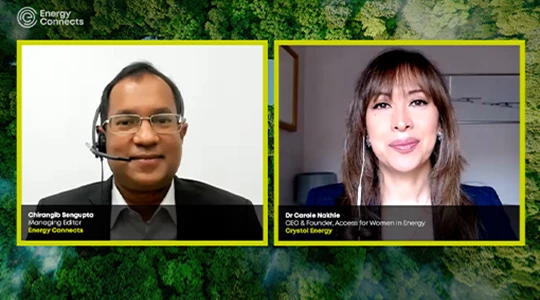
More women in energy vital to the industry’s success
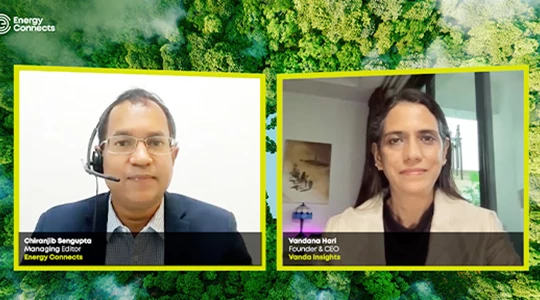
India’s energy sector presents lucrative opportunities for global companies
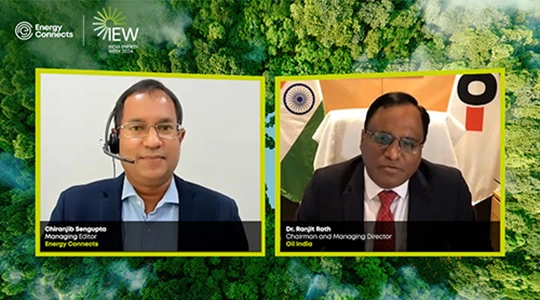
Oil India charts the course to ambitious energy growth
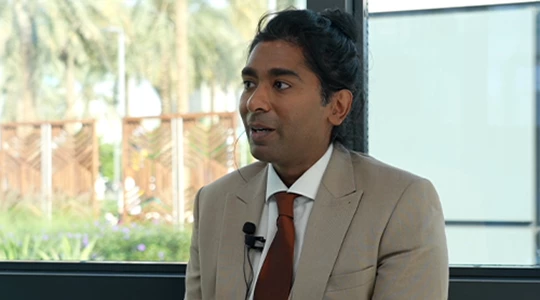
Maritime sector is stepping up to the challenges of decarbonisation
Partner content
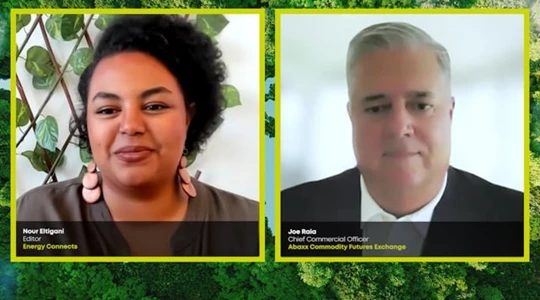
Navigating the trading seas: exploring the significance of benchmarks
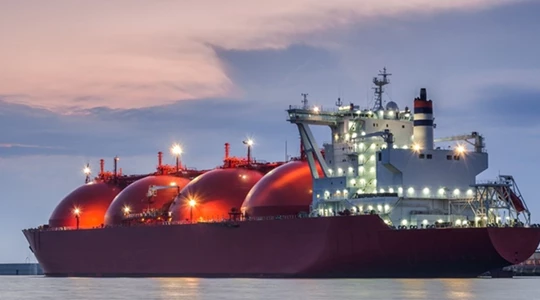
Back to the Future(s): the best commodities benchmarks are still physically settled
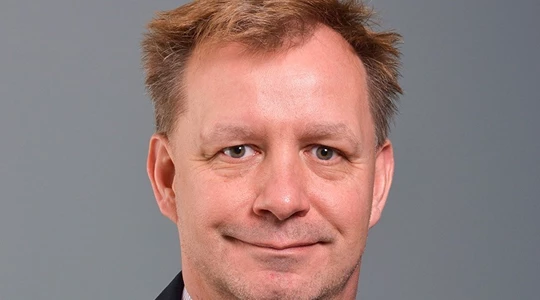
Ebara Elliott Energy offers a range of products for a sustainable energy economy
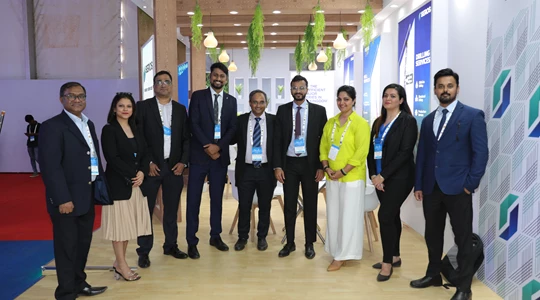
Essar outlines how its CBM contribution is bolstering for India’s energy landscape
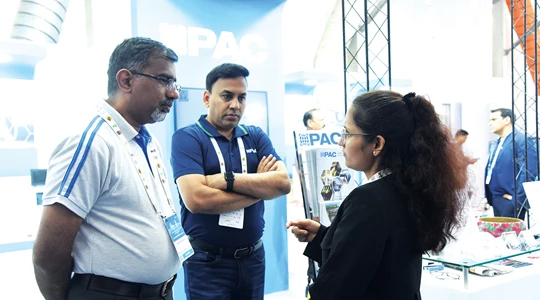