Interchangeability - key to efficiency and sustainability for sand management
Production engineers have long viewed sand control as an undesirable, expensive and complex procedure that has been compounded by volatile market conditions and demands for greater efficiency and sustainability. It can damage downhole subsea equipment and surface production facilities, and also increase the likelihood of catastrophic failure.
The ability to cross-utilize interchangeable inventory has a major impact on the amount of equipment needed to address multiple projects simultaneously as well as the need for contingency planning. Thereby, minimizing the amount of material used with minimal logistics.
To contribute to a sustainable future for the oil and gas sector, where efficient use of resources is vital, Tendeka has adopted an inflow “plug and play” approach to sand and inflow control with interchangeable inflow equipment supply and fitting.
Standardizing products and methods
With many different sand control approaches designed for varying reservoir conditions, selecting an appropriate technique or technology depends on whether sand control is needed to dictate if the chosen route is successful.
The process involves the standardization of equipment whilst still maintaining flexibility in the design. This means that the same chassis can be used for multiple applications and customized immediately prior to installation to optimize reservoir performance. A smart control framework to manage sand production and inflow control will consider the most efficient combination of screen filter size, type, and mechanical rating selection. The benefits of this approach include:
- Improved reservoir performance: flexible “plug and play” approach allows for final sand and inflow control design to be optimized at the rig site based on the latest reservoir and formation evaluation data
- Minimized tooling and machinery adjustments leading to improved manufacturing efficiency
- Minimized waste through repeatability and reliability
- Efficient supply chain and material management by using metallurgy suitable for producers and injectors
- Streamlined manufacturing process
- Flexibility due to re-use of raw materials when plans change.
Streamlining manufacturing
Key to the process is supplying the equipment ready to house multiple solutions. Each joint of sand screen with inflow applications comes supplied with between one and four tapped apertures that can be configured to have any combination of valves. These apertures can accept Tendeka’s FloSure autonomous ICDs, FloRight and FloExtreme ICDs, FloSure injection valves, FloCheck control valves, blanking plugs, or even fully open ports in some cases. These can be changed prior to mobilization or on site depending on well conditions.
Tendeka’s approach is to standardize the lengths and material grades of the screen jackets utilizing inflow control devices which constitute by far, the majority of the screens produced by the company. This significantly reduces manufacturing costs and the waste created during construction.
To include ICDs for the mesh and wire wrap jacket screens, the proposed default length would be 4.8m (16ft) or 7m (23ft). ICD and outflow control devices include the passive, autonomous and advanced ICDs, as well as check valves. Material grades are also standardized. The most common being 316 alloy, while 825 alloys are also used for more corrosive and challenging wells, depending on downhole environment, lower completion pipe grade chosen and expected service life.
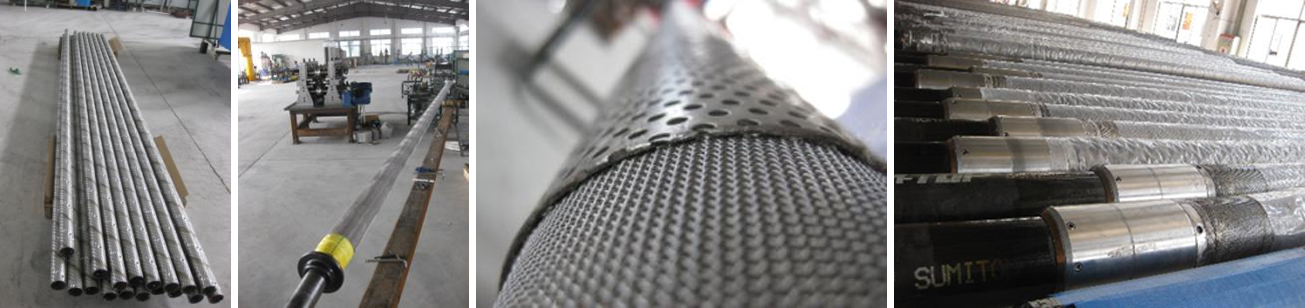
Figures 1: The 7m jackets (left to right) are fitted with layers of the premium mesh screen jacket with an outer shroud on the outside and a drainage layer underneath.

Figure 2: Passive inflow control devices allow flow in both production and injection directions.
Should the autonomous inflow control valve be considered beneficial for production optimization, Tendeka’s range of injection valves can be used alongside to allow fluid injection in each zone and also differentiate the pressure/flow rate response in both directions as desired.
Additionally, as screens are designed with robustness in mind, it has been possible to implement and adjust processes to minimize waste. For example, removal of protective packaging material onshore to reduce waste handling at offshore locations.
As an example, by eliminating the necessity to change length and OD of every ten screens, the advanced completions and production optimization specialist can build about 35% more screens per day than if a customized design was needed. Most notably, the percentage of custom-built screen designs beyond the proposed scope declines each year due to this “plug and play” philosophy.
“Plug and play” philosophy
Bespoke designs remain a vital factor to address certain production challenges. However, the percentage of custom-built screen designs out with the proposed scope declines each year due to the “plug and play” philosophy.
Having the two standardized M33 ports allows Tendeka to produce around 48 different combinations of valves for oil producers and about half for water injectors. This means a vast range of possible inflow areas and pressure responses within screens in different zones of a single well. As a novel and flexible approach, this allows last-minute changes to well completion design where decisions are being made ‘live’ as the logs are being received on the actual drilled well trajectory and zones passed.
This agile approach can enhance decision-making to select or swap, at the most appropriate interval, inflow, outflow or check valve devices to counter saturation, possible sand production, porosity, and permeability, at any time.
Interoperability - case study
Located in the Norwegian Continental Shelf, optimization of the completion strategy for a single horizontal attic infill well was possible due to the flexibility of using sand screens with interchangeable inflow control devices. AICDs were used to close the gas cap and to design inflow linked to estimated oil per drainage area.1
As the middle part of the well showed some gas intervals and a limited oil column this was blanked. In the toe part, without free gas, passive ICDs were used. Consequently, the operator decided to install larger AICDs (7.5mm) instead of ICDs here to provide insurance against massive gas inflow and create an environment with lower pressure drops in the deeper sections. Flow would then come into the 5mm AICD combinations (single or double) in the heel section. These were adjusted for each compartment based on the reservoir properties within.
The AICD gave somewhat better selective choking on water and much better selective choking on gas and high GOR mixed flow, as compared to the ICD. This, together with the ICD/AICD dimensions that were available offshore to obtain optimal oil inflow, was the background for the installed lower completion.
Tracers were mounted in the sand screens to monitor clean-up, inflow per zone and the onset of water production and indicated good clean-up of the entire well. The steady state inflow model was used extensively in the execution and review phases.
The initial well performance with no water and low free gas amounts gave a larger pressure drop than expected. A later tracer-based chemical PLT gave slightly different results than expected. Pressure data, tracer data, log data and the effective multiphase AICD model were thoroughly investigated to derive scenarios, that could explain this discrepancy. The most likely scenario gives a good history match for both pressure and tracers and gives extra insight into key reservoir parameters, zonal inflow and the effective behaviour of the AICDs during multiphase flow.
The well has exceeded pre-drill production rate expectations, despite the larger than expected pressure drop. This is partly explained by the autonomous ICDs choking on gas inflow along the wellbore.
Efficient material and inventory management
A standardized product range with fixed dimensions covering most of the applications requirements, allows for shorter lead-time and more efficient and cost-effective manufacturing, which then transfers to the price of the part (Figure 3).
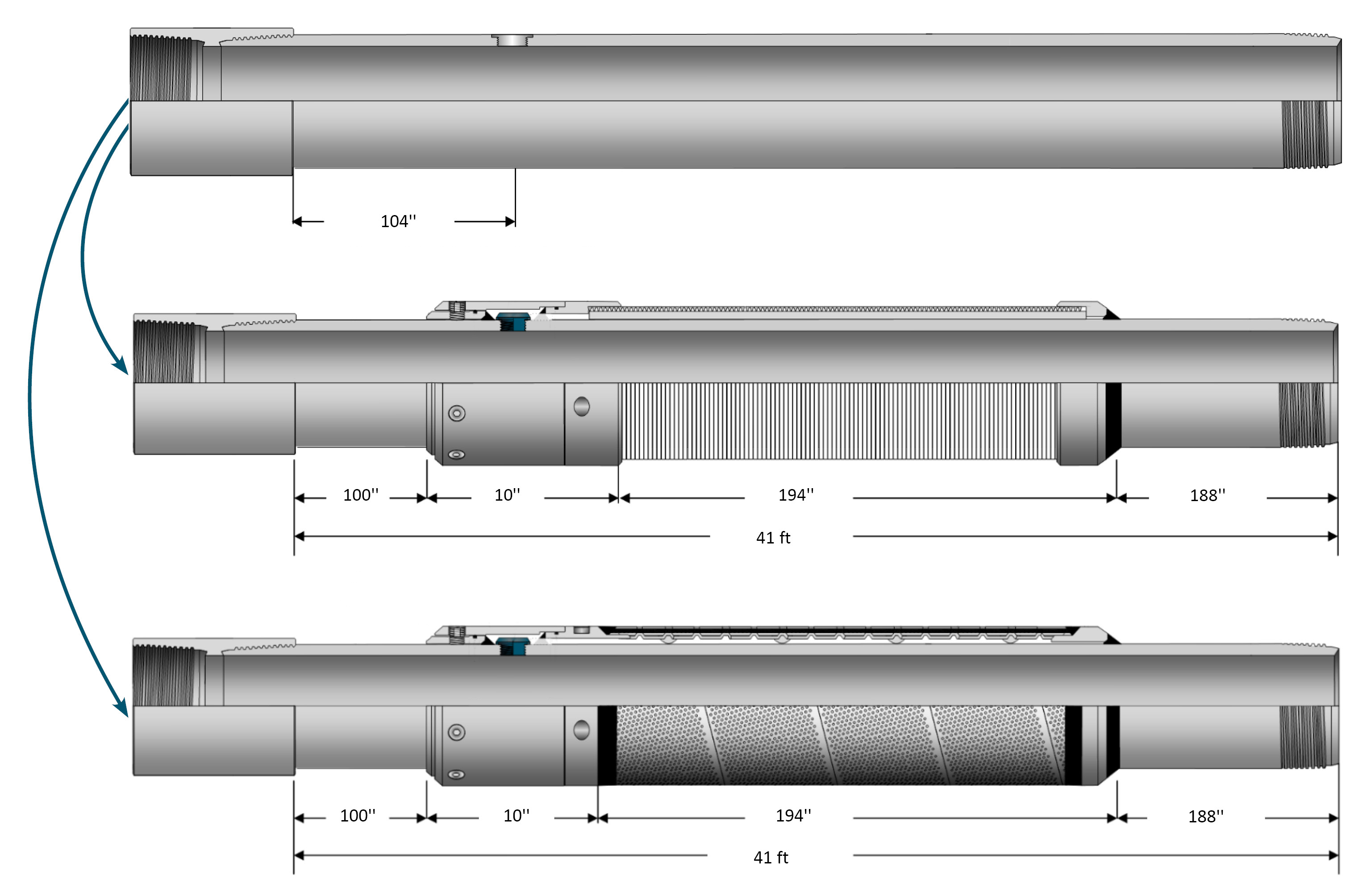
Figure 3: Standardized dimensions and “plug and play” design built around doubled M33 port allows streamlining the manufacturing process for all types of sand screens.
Inflow control interchangeability allows standardized screens to be utilized by the operator at different asset/campaigns and sometimes, different wells than originally planned.
Assuming the sand properties remain within product’s optimal performance range, they can be changed at any stage of screen handling before running in hole. This is a game changing ability for an industry now more focused than ever on efficient, sustainable, optimum performance.
Energy Connects includes information by a variety of sources, such as contributing experts, external journalists and comments from attendees of our events, which may contain personal opinion of others. All opinions expressed are solely the views of the author(s) and do not necessarily reflect the opinions of Energy Connects, dmg events, its parent company DMGT or any affiliates of the same.