Redefining the roles of the world’s refineries
By: Luigi Crolla, Principal Process Engineer, UK and Europe at SNC-Lavalin and Scott Shorey, Global Director, Petrochemicals, Europe & America at SNC-Lavalin
Sixty-seven countries and eight US states have a Net Zero ambition. This effort needs to be on a global scale and the world will need to transition to low carbon and no-carbon energy; a process of weaning our economies away from fossil fuels and decarbonising energy. Extensive research shows the practical considerations of decarbonising power generation but how do we decarbonise fuels and chemicals?
The need for change
By 2030, 14 percent of current refineries operating in advanced economies face the risk of either being used far less or closing down. By 2050, this number could grow to 50 percent as the transition from fossil fuels to electric vehicles ramps up. Traditional refineries are already being integrated with petrochemicals production; however, many remain configured to produce only traditional transportation fuels. The role of those that produce gasoline, diesel, aviation kerosene, and fuel oils must be reassessed. Chemicals are required for many of the products that make our civilization possible (e.g. polymers / plastics) and are fossil based, but they must now be produced sustainably. To remain economically viable, refineries must adapt to a decarbonising world.
Blue hydrogen and producing sustainable fuels and low carbon chemicals offer a future by using a diverse range of feedstocks such as biomass. There is no one technology to deliver the perfect green fix, but a broad framework of technologies, based on choice, scale up, government policy and regulations.
Driving for change
There are different drivers towards a change in energy usage and its sources: financial, policy, and moral.
Approximately 80 percent of the energy consumed by the US in 2020 came from fossil fuels. Renewables amounted to only 11 percent of the energy consumed and of that, total solar and wind power was 36 percent. While energy-related CO2 emissions were only 2 percent above 1990 levels, the US is nowhere near Net Zero today. US refineries process a diet of conventional crude oils and produce predominantly conventional transportation fuels. Integration with other business sectors (e.g. petrochemicals) remains mostly hydrocarbon-based.
In the UK, less than 5 percent of energy used in homes is from low carbon sources; the aviation industry has no commercial low carbon planes; less than 1 percent of all kilometres driven is done via a low carbon/electric vehicle. Future legislative changes will mean the UK’s refineries will be underutilised as society moves away from using traditional transport fuels – e.g. the planned ban on new car sales over the coming decades in Norway, France, and the UK. Yet some industries will always require long distance travelling and surface transport such as HGVs, which still require a low carbon alternative.
The average greenhouse gases saving from biofuels was 74 percent in 2015-16: 2.67 million tonnes per annum of CO2 or equivalent to taking approximately 1.3 million cars off the road. Europe’s biofuel production capacity is expected to grow to around 8 million tonnes per year from the current 3 million.
There are policy and financial shifts with major energy companies developing low carbon strategies, but more importantly there’s a moral obligation to society, future generations, and the security of the world’s resources. Public perception of fossil fuels and conventional hydrocarbon sources varies significantly by country; natural gas is consistently seen most positively with crude oil and coal seen quite negatively. This world view is certainly impacting community and local authorities’ tolerance to developing sites seen as ‘polluting’.
Feedstocks and low carbon products under pressure
Feedstocks is the input material: wood, biomass, tyres, virgin oils, used cooking oil, plastics, municipal solid waste, commercial and industrial waste, refuse derived fuel, solid recovered fuel. Low carbon products are aviation kerosene, petrol, diesel & HVO, synthetic natural gas, bio liquid natural gas, low carbon hydrogen, naphtha, electrons, and processed with CO2 being captured and stored.
The growing need for sustainable fuels, resulting in increasing demand for easier-to-process low carbon feedstocks, has put pressure on supply. Demand will outstrip supply of these feedstocks (the supply does not match that available for crude oil). With this scarcity and variability in demand, there is a clear need for flexibility in process and production methods. The ability to design for a range of feedstocks would allow capital invested in new plants to be adaptable for future feedstock availability.
The low carbon plants being developed today tend to be smaller in scale and aimed at a single feedstock, producing one or two products. Without the economy of scale, the infrastructure and utility costs associated with these plants will likely be a higher percentage of the capital costs compared to a refinery with many units.
Being flexible in the process with a Low Carbon Multi-Unit Plant (LCMUP)
To access a wider variety of feedstocks, gasification and pyrolysis processes could convert a variety of feedstocks to a pyro-oil or syngas - both are well understood and proven pathways for producing intermediates for the petroleum and chemical industries. Syngas can also be produced using natural gas using CO2 capture to reduce the carbon footprint.
A LCMUP can help tackle global waste by gasifying solid wastes via known technologies such as a fluidised bed reactor and partial oxidation units. Feedstocks such as waste plastics and waste tyres are chemically transformed using a pyrolysis reactor to develop pyro-oils.
While additional units would be required to process feedstocks to treated syngas and pyro-oils, the infrastructure and utilities are in place at existing refineries to support them. By maintaining the flexibility of processes and methods, a LCMUP refinery could flex with future market demands, which it certainly will have to do over the next 30 years.
Location, location, location – a set of criteria for a LCMUP:
- Access to sea, rail, and road transport for feedstock supply and product delivery
- Proximity to services – water, power, effluent, pipelines
- Existing infrastructure, administration buildings, control, on site utilities, tankage
- Proximity to population – close to retail markets, workforce, operations, maintenance, contractors, local authorities and communities
- Hazard management
- Access to first wave carbon capture and storage clusters
Balancing a need for fuels with changing public perception requires taking communities on a pragmatic journey. Refineries are experienced in engaging with local stakeholders and, that communication needs to evolve, as the industry transitions to a clean greener format.
While refinery projects are expensive, on a per ton of product basis they are extremely economical due to scale and decades of design practices and standards. Today’s most modern refineries employ expensive, high-pressure processes (e.g. hydrotreating and hydrocracking) to produce clean fuels. Refinery standards for hydrotreating or the handling of feedstock are tailored to the process hazards associated with refinery operations; they’re best placed to handle high hazard process units to produce fuels, e.g. hydrogen. However, all involved in low carbon projects should challenge the standards to be applied to lower hazard and more industrial processes to deliver more cost efficiently.
When to start?
If 2030 is the aspirational horizon for such low carbon projects, then project lifecycles (around six to seven years) need to begin now and industry can’t afford to wait. Refiners know how to project future requirements, source feedstocks, run higher hazard plants, and are well linked into the delivery chain of fuels and chemicals. By building in flexibility at the front end, a LCMUP refinery can remain economical in a world of variability across low carbon feedstocks.
The future of refineries is under pressure in the journey to Net Zero, but society still needs their expertise, products, and chemicals. The task of reassessing their role and adaptation to a decarbonising world, show their worth to industry, the workforce, and remain economically viable is not one to deliberate over.
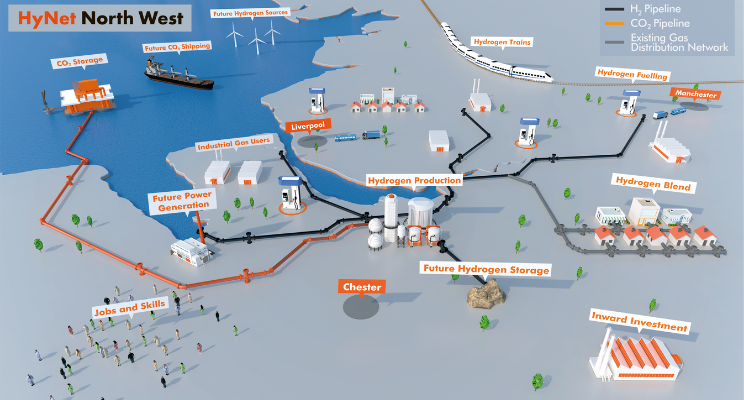
Energy Connects includes information by a variety of sources, such as contributing experts, external journalists and comments from attendees of our events, which may contain personal opinion of others. All opinions expressed are solely the views of the author(s) and do not necessarily reflect the opinions of Energy Connects, dmg events, its parent company DMGT or any affiliates of the same.