Accelerating customer performance in the energy transition
The use of integrated renewable energy solutions for the marine industry is a topic that is gaining momentum. What is Siemens Energy doing to help mitigate maritime emissions?
We have developed and commercialised several innovative technologies used to enhance the sustainability of marine operations.
One example is our SISHIP BlueDrive PlusC propulsion system, designed to reduce emissions from diesel-electric or all-electric vessels by enabling individual speed control over engines. In the case of diesel-electric ships, BlueDrive PlusC allows engines to operate at variable speeds, which reduces specific fuel oil consumption and associated emissions. In addition, energy storage solutions, like our BlueVault lithium-ion energy batteries, can easily be integrated to enable hybrid operation.
Dozens of ships ranging from passenger ferries to platform supply vessels have BlueDrive PlusC installed. One of its earliest applications was on the world’s first all-electric car and passenger ferry in Norway, named Ampere.
Earlier this year, you announced a collaboration with Sweden-based Liquid Wind AB to accelerate carbon-neutral marine transportation by scaling up renewable methanol production. When do you expect to bring renewable methane to market at scale?
Together with our partners in Liquid Wind AB, we are taking over a first mover’s role in decarbonising the marine industry by planning Scandinavia’s first commercial scale eMethanol production facilities.
Siemens Energy will provide a 70-Megawatt PEM-Electrolyser for the project that will use renewable electricity to split water into green hydrogen and oxygen. The green hydrogen will be combined with biogenic CO2 to yield carbon-neutral methanol, replacing hydrocarbon-based fuels in shipping applications. The construction process is scheduled to begin in spring 2022. Once operational, the facility is expected to produce 50,000 tons of green methanol starting in 2024, with 10 additional plants planned through 2030.
We also see opportunities to use eMethanol for non-marine applications, for example, to drive de-fossilization of industrial facilities, such as refineries, power plants, pulp and paper mills, and others.
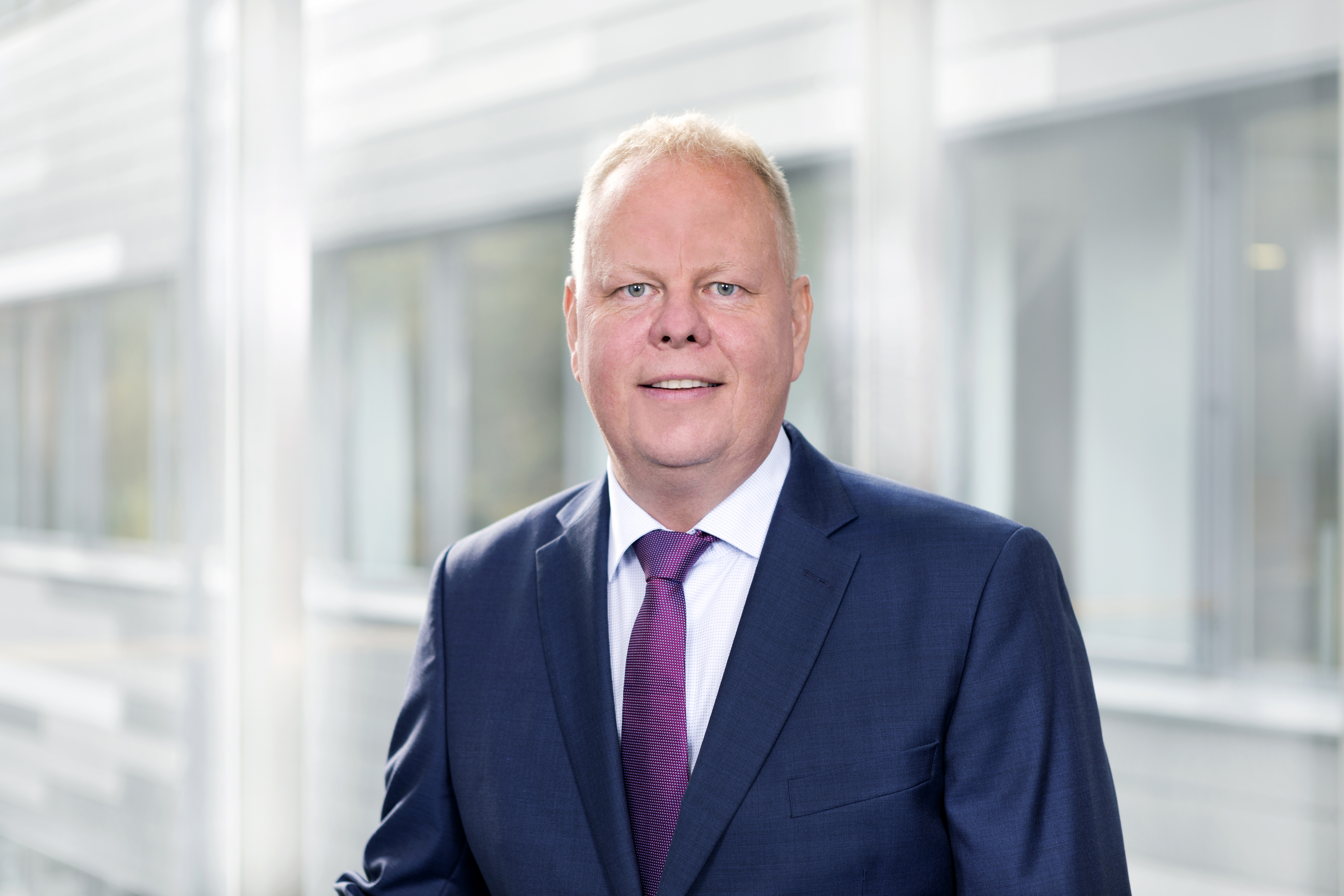
Thorbjörn Fors, Executive Vice President of Siemens Energy Industrial Applications Business.
We see more activity and discussion around carbon capture technology, especially in the petrochemical sector. Is this an area Siemens Energy plays in?
Yes. We are seeing an increasing number of customers come to us early in the FEED phase of projects to design equipment configurations to operate within the constraints of specific carbon capture technologies.
This year, we also announced a collaborative agreement with Aker Carbon Capture to develop combined offerings for carbon capture solutions that can be applied to gas turbines and gas-fired power plants. The collaboration will initially focus on new and existing low-carbon power generation. A combination of new turbines and carbon capture and storage (CCS) can provide sustainable solutions.
We certainly can’t talk about digitalisation without discussing cybersecurity. How is your business ensuring cybersecurity for customers in an era of data-driven operations?
You are correct. Cybersecurity must be at the core of every aspect of companies’ digital transformation strategies. It’s our license to operate, so to speak.
Today, one of the biggest challenges the industry faces is visibility. Managing and securing the complexities of today’s digital ecosystem requires cyber security-based artificial intelligence (AI) to provide context and visibility across industrial operating environments.
We recently launched a new AI-based solution for monitoring and responding to cyber threats in industrial applications – called Eos.iiTM. The platform collects and collates data flows from IIoT endpoints, automatically tailors defensive practices, and prioritizes high-impact events with the assistance of machine learning algorithms. Its goal is to provide customers with an evergreen foundation for industrial cybersecurity.
Additive manufacturing (AM) is often talked about when it comes to digital technologies and solutions. How, specifically, is the Industrial Applications business using AM to help accelerate customer performance?
There are several areas where we are leveraging AM. One example where it is generating significant value for our customers is in manufacturing gas turbine components.
There are virtually no limitations in terms of what we can design and build with AM. We can create very intricate single-piece components without brazing or welding, eliminating many constraints of conventional design and manufacturing processes.
AM has already enabled us to realize improvements in our gas turbines' efficiency and fuel consumption. Additional benefits include the potential for longer component lifespan, reduced maintenance costs, and improved availability. Opportunities also exist for rapid prototyping, reduced lead times for spare parts, and serial production of components.
All these developments benefit our customers and positively impact their bottom line.