Autonomously controlling the conformance of fluid injection in carbonate reservoirs
Injecting fluids to enhance oil recovery and/or maintain reservoir pressure presents several challenges including loss of injectivity, premature injector failure, and fluid injection conformance.
Whilst many techniques improve the effectiveness of water/polymer flooding, they have led to insufficient voidage replacement, undesired reservoir pressure profile, the production of unwanted fluids as well as oil left untapped in the reservoir. Remediating such issues is costly and involves complex interventions and re-drills to restore optimum injection performance.
Tendeka, a TAQA company, has developed FloFuse, an interventionless, injection rate-limiting, autonomous outflow control device (AOCD) which can mitigate the conformance issues for both fluid injection and/or acid stimulation operations particularly in carbonate reservoirs (Figure 1).
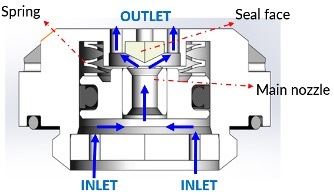
Figure 1: The AOCD design with two operational positions
The technology was recently deployed in a water injection well in a carbonate reservoir in the Middle East which was accumulating excessive water across some sections due to faults and fractures. By restricting flow into the thief zones and ensuring proportional distribution of injection fluids along the full length of the wellbore, the project demonstrated how the completion can be used for improving the performance of injection operations.
Controlling conformance
Conformance issues attributed to injection wells in carbonate reservoirs is related to the continuously changing well injectivity profile. Amongst many factors, the dilation/growth of natural fractures is proven to have a significant impact which can ultimately impact performance.
To manage this issue, many operators have used passive inflow control devices (ICDs) with or without sliding sleeves and/or more complex interval control valves (ICV) completion. The ICDs are installed as a segmented lower completion string in horizontal/vertical injection wells to balance water outflux from the well to the reservoir. Though proven to improve fluid conformance in sandstone reservoirs, their functionality is limited in carbonated reservoirs with complex pore and dilating fracture systems.
Optimising injection operations
Like other flow control devices, the AOCD is installed as a segmented lower completion string across several zones in the horizontal/vertical injection well. It has two operating conditions:
- As a conventional flow control device
- As a barrier when the flowrate through the valve exceeds a designed limit.
Once the pressure drop in the formation decreases as a result of increased injectivity of a fracture or high permeability streak, the injection rate into that compartment will rise. The resultant increased pressure drop through the nozzle at that section of the well acts against the return spring until the flow area between the seal face and the nozzle becomes restricted and the device triggers to the closed position restricting the outflow into that zone. Here, the denied fluid to that specific zone will be distributed among the neighboring regions. This prevents excessive fluid injection into the thief/fracture areas and maintains a balanced or prescribed injection distribution.
Figure 2 shows how injection outflow passes through the normal operating nozzle into the housing and through the screen.
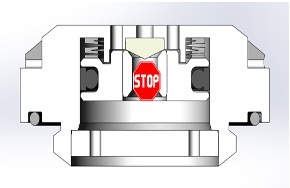
Figure 2: The AOCD mounted in the screen housing and flow path
The AOCD is fully reversible and will re-set if the rate becomes sufficiently distributed again. The target normal operating rates and degree of outflow control and trigger rates can be varied by application.
Proven field performance
The single biased open valve has undergone full-scale laboratory tests as well as numerous single-phase injection experiments including gas, water and polymer to define the characteristics of the device with different sizes. For example, the plotted data in Figure 3 represents the pressure drop across the device as a function of flow rate for single-phase water across the varying nozzles sizes. Based on the results, it shows that after reaching a certain flow rate, FloFuse shuts off water flow. This trigger rate is dependent on the nozzle size and spring constant.

Figure 3: The performance of AOCDs with water
The AOCDs were recently installed as a retrofit solution in an injection well in a carbonate reservoir in the Middle East. Initially completed as a dual completion in 2012, the short string (completed as a cased and perforated completion) injected water into the upper layer of reservoir B while the long string (kept as a 6” open hole) injected water into the lower formation. The well was characterized by low to moderate reservoir properties with an average matrix permeability of 4.8mD. With an average injection rate of around 3,000BWPD, the main objective of this well, plus three other neighboring wells, was to maintain the reservoir pressure of reservoir B.
After two years, the well was taking a greater volume of water than expected at some sections. This was due to its location intersecting two interpreted faults as well as ant-tracks or potential fractures or faults: the behavior and properties were uncertain.
Approximately 36% of total water injection was expected to be received by these low injectivity sections. Few other sections were taking a higher portion (64%) of injected flow rates, confirmed by PLT.
FloFuse was selected as it automatically responds to dynamic changes in intake rates and unexpected variations in fluid displacement by restricting the injection of excessive fluid into fractures and faults. After performing an extensive modelling workflow, the completion consisted of nine joints of AOCDs, five joints of bypass high-pressure resistance ICDs and five swell packers, installed via workover.
Based on the comparison between old and new PLTs, it was determined that the injection rate into
the zones with fault and ant-tracker features was reduced by 42% while water injection in the other zones increased by 20-25%, with no suspected faults and very low injectivity, was achieved. As a result, the overall sweep efficiency in this section significantly improved. Moreover, water injection contribution along the horizontal section of the hole was better.
As this type of completion can function as mechanical diverters, an acid stimulation operation is planned in the well in the near future to help improve the injectivity of zones with low permeability and remove any skin accumulated over years of injection. This would further improve the water injection conformance of the zones.
Conclusion
Since its introduction in 2019, AOCD technology has been used on numerous field applications worldwide and is proven to:
- Reduce injection cost
- Improve field NPV (net present value)
- Ensure reliability of injection well systems
- Control conformance and manage uncertainties
- Lower the risk of poor conformance.
Research and field application have demonstrated that the adjustable capabilities of the device make it an ideal completion for most injection operations including water injection wells, polymer injection wells, acid injection stimulation operations as well as water alternating (WAG) operation and carbon dioxide (CO2) injection/storage wells.
KEEPING THE ENERGY INDUSTRY CONNECTED
Subscribe to our newsletter and get the best of Energy Connects directly to your inbox each week.
By subscribing, you agree to the processing of your personal data by dmg events as described in the Privacy Policy.